Lost wax casting process:
Lost wax casting (also known as investment casting or precision casting) is a casting process that injects liquid wax into a metal mold to make a wax model consistent with the casting, and then wraps it with several layers of refractory ceramic materials such as clay and heats it. The wax is melted and flowed out to obtain a hardened empty shell formed of refractory material. The hardened ceramic shell is roasted, and the molten metal is poured into the mold shell. After the metal cools, the mold shell is crushed to obtain a metal casting.
The term investment casting comes from the process of heating and melting wax in a mold shell. Investment casting is often more popular than other casting processes because investment casting castings have high dimensional accuracy and good surface roughness. They can be thin-walled parts or parts with complex internal and external structures, and unlike sand casting, they do not have to be drawn. Die slope.
Investment casting materials are widely used, such as carbon steel, alloy steel, stainless steel, etc., and can also be non-ferrous metal materials, such as aluminum or copper and other alloys. In the field of thermal processing, investment casting can be used for parts that are difficult to obtain or difficult to form, as well as some forged parts with high processing costs. In the field of casting, investment casting can be used to replace other forms of casting for some products to reduce processing. Cutting allowance reduces costs, improves dimensional accuracy, surface roughness and mechanical properties of materials, thereby achieving the purpose of upgrading product grades.
Investment casting process:
The investment casting process includes several steps: metal mold making, wax pattern production, mold shell making, casting, sand cutting, and grinding and finishing.
1. Metal mold manufacturing
Both the wax pattern and the mold shell need to be destroyed during the investment casting process. Each casting requires a new wax pattern, so a mold for the wax pattern needs to be made.
Making the mold requires full consideration to calculate the shrinkage, which is reflected in the wax pattern and mold shell and in different processes after casting.
2. Wax pattern production
The number of wax patterns is always equal to the number of castings to be produced, with each casting requiring a new wax pattern.
The hot wax is injected into the metal mold to cool and solidify. Some complex structures in the inner cavity require the use of ceramic cores to form internal functional structures. A wax pattern is used to produce an exact replica of a part. The production process is similar to die casting, which is molten metal which is liquid wax.
3. Wax model tree
Several wax patterns are welded to wax rods to form a string of wax patterns to form a casting system with a gate on it, which is used to introduce molten steel into the casting system for the next step of the mold shell. .
4. Mold shell manufacturing
Dip the wax mold tree into the silica slurry, and repeat the immersion five or six times. Sprinkle different refractory materials before each immersion, and dry and harden each time. The dry coating is applied to the gate system of the wax mold. A ceramic shell is formed on the periphery. The ceramic shell is heated until the wax melts and drains, and a hollow is formed in the cavity. This completes the production of the mold shell. Investment casting uses many such mold shells.
5. Casting
The mold shell is fired and heated to about 800-900°C. The heating process further enhances the strength of the mold shell, eliminates residual wax or other debris, and evaporates the water in the mold shell.
The raw material (scrap) is smelted in a medium frequency induction furnace, and the alloying elements are batched according to the different materials of each furnace. When the temperature of the molten steel reaches 1530-1580°C, it can be cast. The molten steel is poured into the mold shell while it is hot, poured into the pouring port and passed through The casting system flows into each mold cavity in the tree, and the preheated mold shell allows the molten metal to flow easily through thin-walled or elongated sections. Then after it cools and shrinks, a high-precision casting can be obtained.
6. Clean sand cutting
After the cast mold shell and casting are fully solidified and cooled, vibration equipment is used to separate the mold shell from the casting. After preliminary sand cleaning, a shot blasting is carried out, so that the sand on the surface of the casting blank is basically removed, and then the individual castings can be separated from the casting system through different cutting methods.
7. Gate grinding and finishing
To remove the gate residue from the blank casting, it is mainly grinded by grinding with a grinding wheel or machining. This process is divided into preliminary grinding and fine grinding. The body of the part should not be damaged during grinding. Subsequent finishing is mainly to repair some surface defects that may exist on the surface of the casting, such as sand holes, slag holes, flash burrs, bulges, deformation, etc. The main methods are grinding, welding repair, shaping and shot blasting.
After passing the appearance inspection, the castings are transferred to the heat treatment production line for heat treatment in different processes
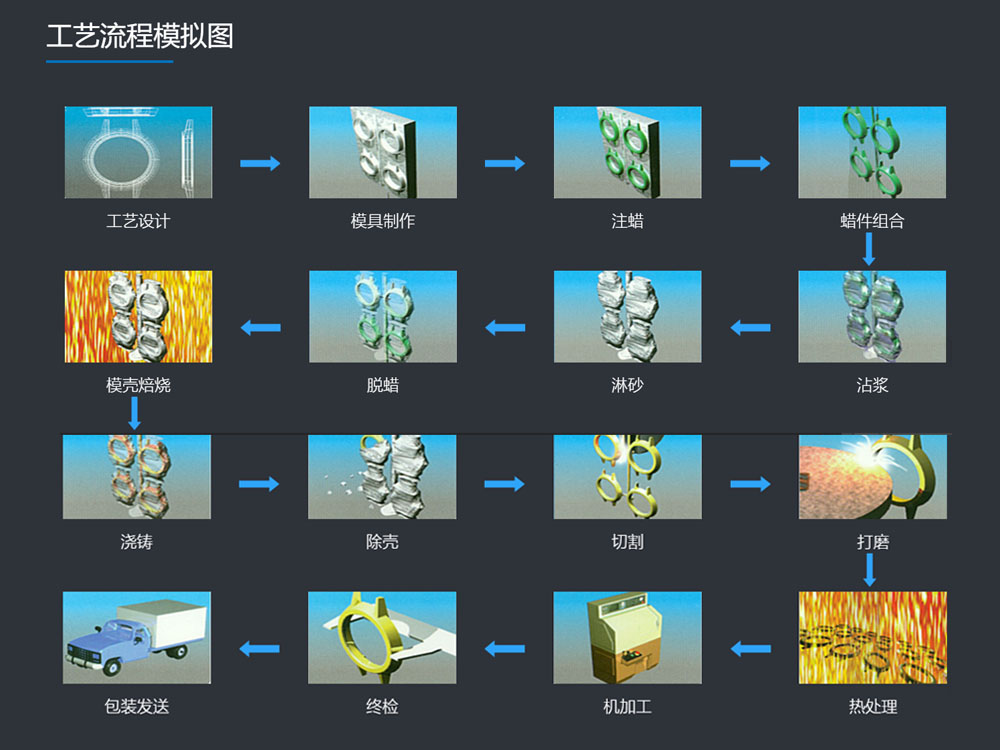
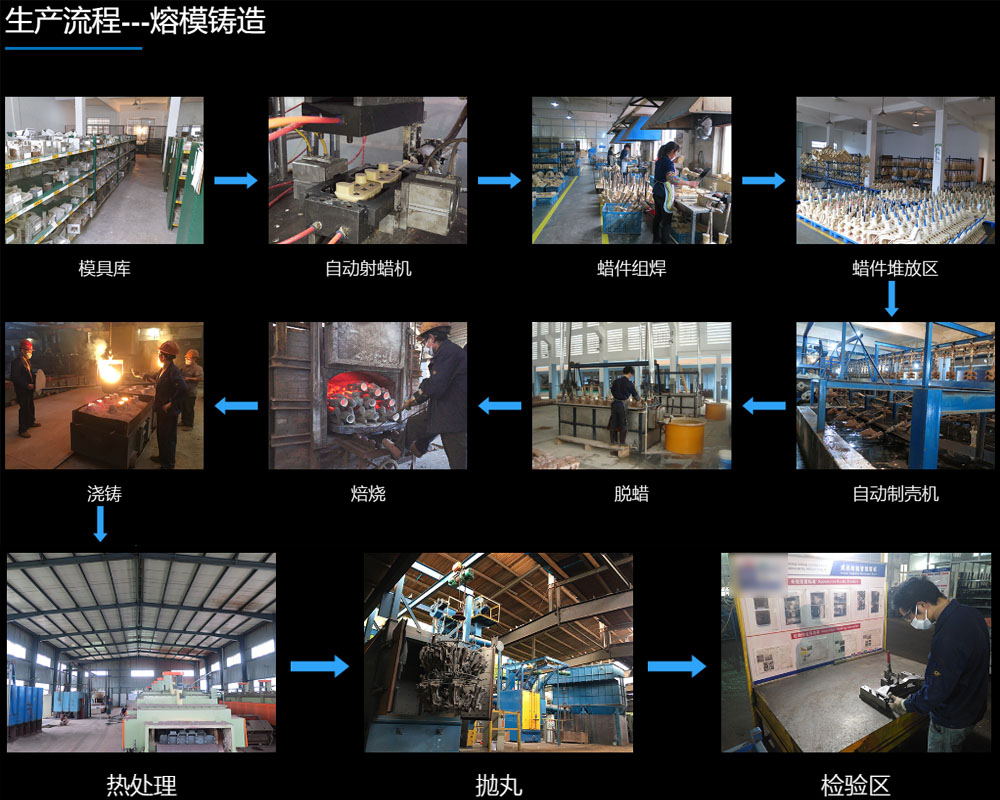
3D printing technology is now also used in the casting field. Wax molds are traditionally used for investment casting. In addition to wax molds, Harbin 3D has also developed photosensitive resin that can be used for casting, so that it can be used with SLA3D printers to directly produce original models. 3D printing can more efficiently produce accurate and complex prototypes. This is particularly valuable for manufacturing high-precision parts with complex geometries. Currently, Harbin Engineering 3D's SLA industrial-grade 3D printer uses casting resin to print complex workpieces and has successfully produced metal castings.